COMPANY
(注意)本記事は、金剛株式会社が1991年8月10日に発行した機関誌「PASSION VOL.8」の内容を、当時の記録として公開するものです。記事内の情報は発行当時のものであり、現在の状況とは異なる場合があります。また、当時の社会情勢や倫理観を反映した表現が含まれている可能性があり、現代の基準に照らし合わせると一部不適切と感じられる箇所もあるかもしれませんが、資料的価値を考慮し、原文のまま掲載しています。掲載されている商品やサービスは、既に販売・提供を終了している場合があります。
本記事は、著作権法上の引用の範囲内で掲載しています。当時の記録として、皆様に楽しんでいただけましたら幸いです。
移動棚で培った技術をAGVSに
(株)日立物流九州営業部 福岡配送営業所殿に、金剛(株)が製作した「有軌道AGVS (Automatic Guided Vehicle System)」を導入いただき、「省力化が実現でき、今ではなくてはならない機器になりました。」とのお誉めの言葉を頂戴しました。お客様に満足戯けるシステムを作り上げることに日夜努力している私共としましては、最高の報酬であり、大きな誇りです。
今回紹介させて戴くのは、金剛(株)が長年培ってきた、移動棚のノウハウを十二分に活用して製作した屋外仕様の「有軌道AGVS」です。目的のために機能を集中させ、機能性・利便性を欲張らなかったことにより、質の高い搬送能力を実現しま した。
別棟に離れた2つの倉庫間を、一回に最高4パレッ トまで荷を自動搬送するシステムで、今まで人手を要 していた搬送作業を省力化でき、しかも荷を乗せてしまえば完全な自動ですので、人手および時間を有効に活用でき、作業の効率化を実現しました。
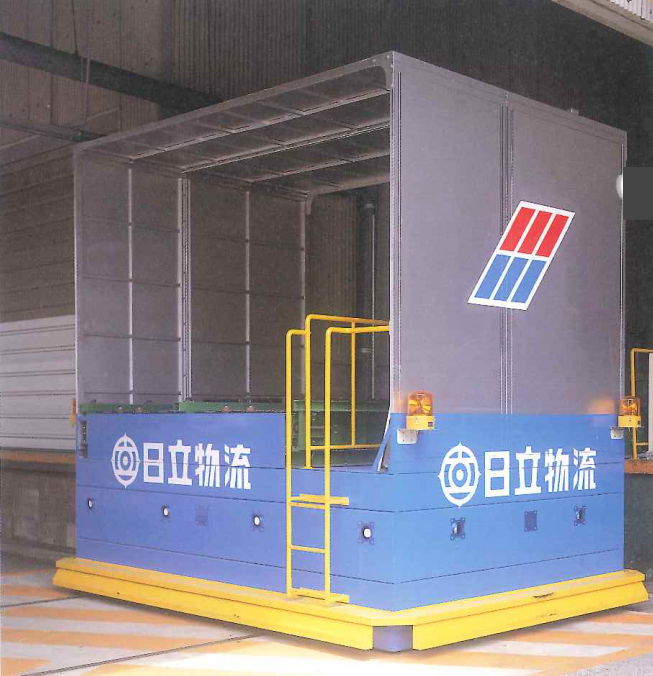
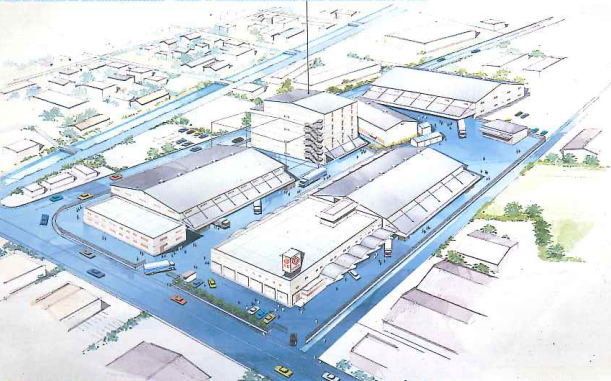
沿革
(株)日立物流殿は、日立グループの製品の物流 業を一手に引受けるために昭和25年、日東運輸(株) として日立市に本社が置かれたのが始まりです。全国各地に営業所を開設し、昭和60年に(株)日立物流と商号を改め、現在では8本部と113の営業所があります。積極的な営業展開により、グループ以外の荷主の割合も年々増加しており、現在では東京第一部に上場、ますますの発展を続けています。
取り扱う品物は、小さな電気部品から家電製品、 オフィス・工場の移転業務までと幅広く、その流通アイテムは数・量ともに膨大です。特に平成3年3月の新宿新都庁の大規模な引っ越し作業では、日通に次ぐ受注を獲得したことが注目されます。
素早く正確な運輸をめざしてー会社概要
名称 | 株式会社 日立物流 |
設立 | 昭和25年2月 |
資本金 | 159億5,540万円 |
代表者 | 小今井傓治 |
従業員数 | 4,358人 |
事業内容 | 自動車運送業、通運事業、海上運送業、荷造梱包業、倉庫業物的流通にかんするコンサルティング業務、建設業、他 |
本社所在地 | 東京都渋谷区渋谷3-6-3 (03)3486-3111 |
本部 | 営業開発本部 茨城営業本部 東部営業本部 首都圏営業本部 中部営業本部 関西営業本部 西部営業本部 国際営業本部 |
売上高 | 1,935億4,500万円 |
九州の物流拠点としての責任ー福岡配送営業所概要
名称 | 株式会社 日立物流 九州営業部 福岡配送営業所 |
所在地 | 福岡市東区和白丘2-1-2 (092)606-2531 |
規模 | 敷地面積:23,218㎡(倉庫面積20,291㎡) |
構成 | 事業所:鉄骨ALC造2F 1号倉庫:鉄筋コンクリート造2F 延4,592㎡ 2号倉庫:鉄骨スレート造2F 延4,123㎡ 3号倉庫:鉄骨スレート造2F 延5,235㎡ 4号倉庫:鉄骨スレート造2F 延4,359㎡ 5号倉庫:鉄骨ALC造3F 延1,784㎡ 6号倉庫:建設中 |
日立のアイディア・正興のフットワーク 金剛の技術
この「有軌道AGVS」の導入以前は、ピーク時でフォークリフト2台を使用し、1パレットずつ揃え場所まで運搬するという形を取っていました。それでも全ての荷の出荷先別荷揃えができず、揃えきれなかった荷をトラックが何度もステーション間を往復して荷を積み込んでいました。トラックの切り返しだけでもロスタイムは大きい上に、混雑時はその切り返しスペースさえない場合もあったとのことです。しかも悪天候時には、荷が濡れる心配からフォークリフトが使用できないという状況で、早急な改善が必要でした。
導入以前の問題点
- 分散して保管していた商品の出荷先別荷揃えに時間がかかる。
- 1PLずつフォークリフト(ピーク時には2台) で荷揃えをしていた。
- トラックの合間をぬってフォークリフトが作業しており、事故の危険性がある。
- 出荷場の手前一列にしか商品を移動できず、 スペース効率が悪く、全ての荷さばきは不可能。
- 作業の流れを中断して荷揃え作業を行なうため、作業の連続性が失われ、ロスタイムが生じる。
- 雨天時には商品が濡れる。
- 荷揃えできなかった商品を積み込むため、トラックが倉庫間で何度も往復している。
- ピーク時には、トラックが往復するスペースが取れず、出荷までのロスタイムが非常に大きい。
導入効果
- 荷さばき時間の大幅短縮。(以前の約50%)
- トラックへの積み込み時間の削減。(以前の 約30%)
- 倉庫間のフォークリフトの往復が減少し、安全性がアップした。
- 商品の集約化によって、情報と商品の一元化が実現。
- 作業に連続性が生まれ、ロスタイムが減少した。
- 悪天候時にも荷さばきが通常通り可能。
- トラックの往復がなくなり、出荷作業に要する時間が削減され、残業時間が減少。
- 将来予想される、取扱い商品の量の増加に対しても、効果が期待できる。
- 運搬業者の肉体的・精神的ストレスの緩和。
(株)日立物流殿では、通常このような業務改善システムを導入する場合、事前に営業開発本部で専門家からなるプロジェクトチームを構成し、綿密な調査を基にプランを立て、企画書を作成します。さまざまなプランをシミュレーションした結果、早い時期から倉庫間に大型の台車を設置するというコンセプトを決定、どのメーカーに発注するのが最適かを検討していました。
今回は、地元九州との関係を大切にしたい、トラブル発生時の素早い対応が必要、などの要望がありました。この条件にあったメーカーの選出を、日立グループと関係の深い(株)正興商会殿に依頼しました。
(株)正興商会殿は、電気・機械・情報通信・空調他の機器などの販売とエンジニアリングをする日立グループの特約店です。ご専門の電気機器のみならず、今後は更に新しい分野をエンジニアリ ングすることを目指し、金剛(株)と代理店契約を結んでいます。(株)正興商会殿の強いご推薦を載き、金剛(株)が今回の有軌道AGVSの開発をお手伝いすることになったのです。
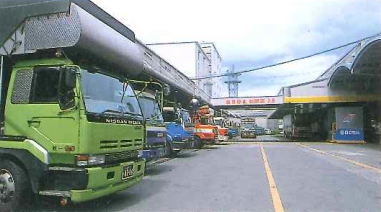
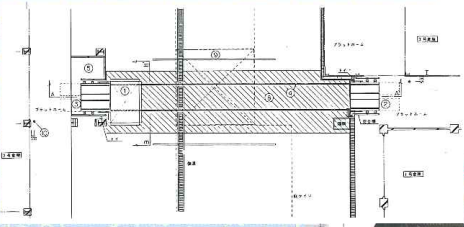
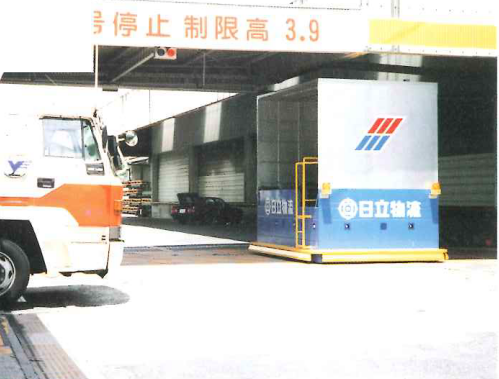
工事範囲
工事面積 :232.4m²
設計管理 :金剛株式会社
施工 :金剛株式会社
工 期:平成3年1月~4月
- レール工事
- 基礎工事
- 無人搬送台車製作
- コンペアステーション設備製作
- プラットホーム増設工事
- 制御・給電トロリーダクト工事
- 信号機工事
- 屋根工事
- 線引き工事(トラマーク、一時停止線)
- ロゴマーク工事
- 台車・ステーション組立、据付工事
- 現地調整、試運転
業務を続けながら雨の合間をぬっての難工事
工事手順は大きく分けて5つの工程に分かれま した。
- 基礎・レール設置:金剛(株)の移動棚専用レールを基本にし、現在まで蓄積してきたノウハウ をいかんなく発揮して設置に取り組みました。 屋外仕様のためレールには切り欠きをつけ、ホコリ、雨水側溝にまとめて流す仕組みになって います。
- 屋根增設工事::AGVSを風雨から保護するために、新たに増設したスレートぶきの屋根で、AGV軌道上を横断するトラック用の信号を取付けました。屋根の内部には、給電用・通信用のトロリーダクト2本を設置しています。
- 入出荷コンペアステーション据付:チェーンコ ンペア、パレットガイド、センサーなどを内蔵したW3,400×D3,400×H1,080 (mm)の大型のス テーションです。
- AGVS本体組立:ステーションと同様、本体の寸法が非常に大きく、また屋外仕様ということで、 防錆塗装は念を入れて行ないました。製作現場にて防錆処理を行ない、さらに組立現場にて再度塗装を施しました。
- 制御関係調整工事:安全性能の充実のため、制御システムの調整は特に丁寧に行ないました。
システム構成
1.AGVS本体仕様
方式 :電動軌道走行式
積載荷重: MAX 2,000Kg (500Kg/PL×4PL)
荷姿寸法: (A) W1,300×L1,200×H2,130
(B) W1,300×L1,500×H2,130
搬送形態: (A) 4PL/台車 (B) 2PL/台車
パレット形態 :木製2方向差し (両面)
AGVS全高 :4,000mm
AGVS全幅 :4,000mm+バンパー
AGVS全長 :2,800mm+バンパー
AGVS積載面高さ: 1,630mm (軌道面より)
走行速度: 18m/min (インバーター制御)
走行距離 :約21m
走行電動機 :1.5Kw (ブレーキ付)
移載方法: チェーンコンベア方式
移載速度: 8m/min
移載電動機 :0.75Kw (ブレーキ付き) ×2ヶ
給電方法: トロリーダクト方式
電源 :220V 60Hz
軌道 (レール) :32角 (23.6m) ×2
軌道間隔: 2,500mm
有軌道 AGVS は本体フレーム、走行装置、移載装置により構成する。
2.コンベアステーション仕様
方式 :チェーンコンベア方式
移載速度: 8m/min
移載電動機 :0.75Kw (ブレーキ付き) ×2ヶ
電源: 220V 60Hz
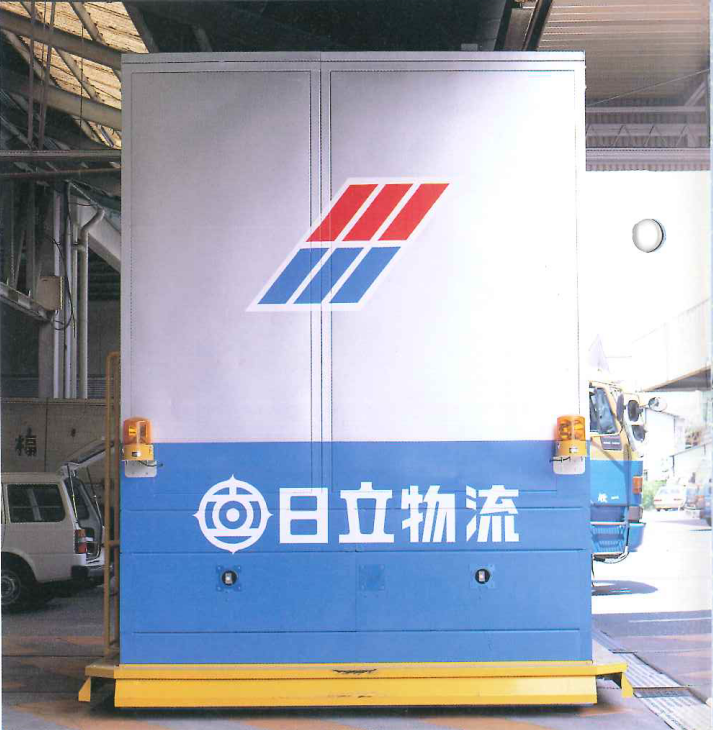
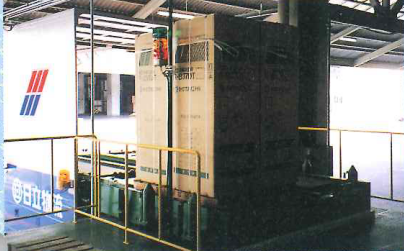
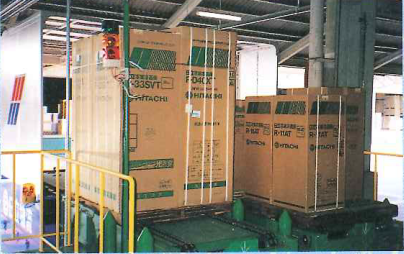
システム運用
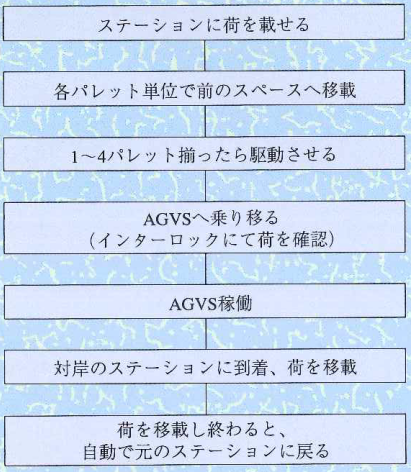
安全対策
走行端強制停止::レール走行端に設けた停止用リ ミットスイッチでオーバーランを防ぐ。
走行端ストッパー:レール走行端に設けた AGVS 暴走防止用。
過負荷検出装置:電動機に規定以上の負荷がかか るとサーマルリレーが作動する。
荷姿検知装置:コンペアステーション上の荷姿の 異常を検知し、コンペアを停止させる。
荷姿定位置検出装置:荷が定位置になければ走行 しない。
安全ストッパー:ステーションのチェーンコンペア 作動時の荷の落下防止のため端部に設けたバー。
インターロック:AGVSとステーションコンベア の受渡し条件が整っていない場合作動しない。
停電対策:停電回復時に再起動しない。
バンパースイッチ:AGVSの4方向に装備。障害 物に当たった場合の非常停止用スイッチ。
パトライト・音声発生装置:走行中はパトライト を点灯し、音声で注意をうながす。
障害物センサー:AGVS前方3m、左右1m以内の 障害物の感知で、連続警戒音を発し停止する。
信号機:AGVSの始動で赤色が点灯し、トラック 通路を過ぎると青色が点灯。
異常時警報装置:異常、緊急停止時にパトライト が点灯し、連続警戒音を発する。
防護欄:コンベアステーションの周囲に設置。
トラマーク・停止線:軌道周辺に引く。
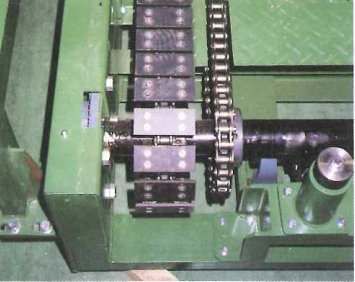
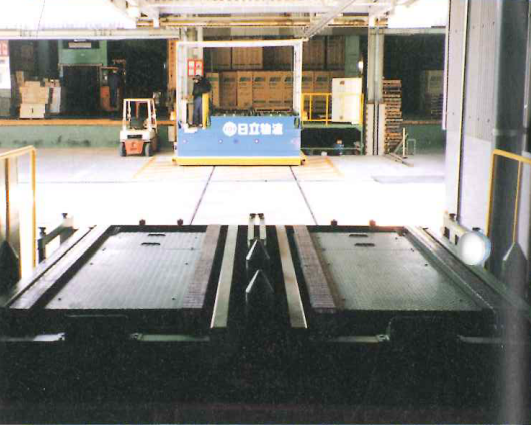
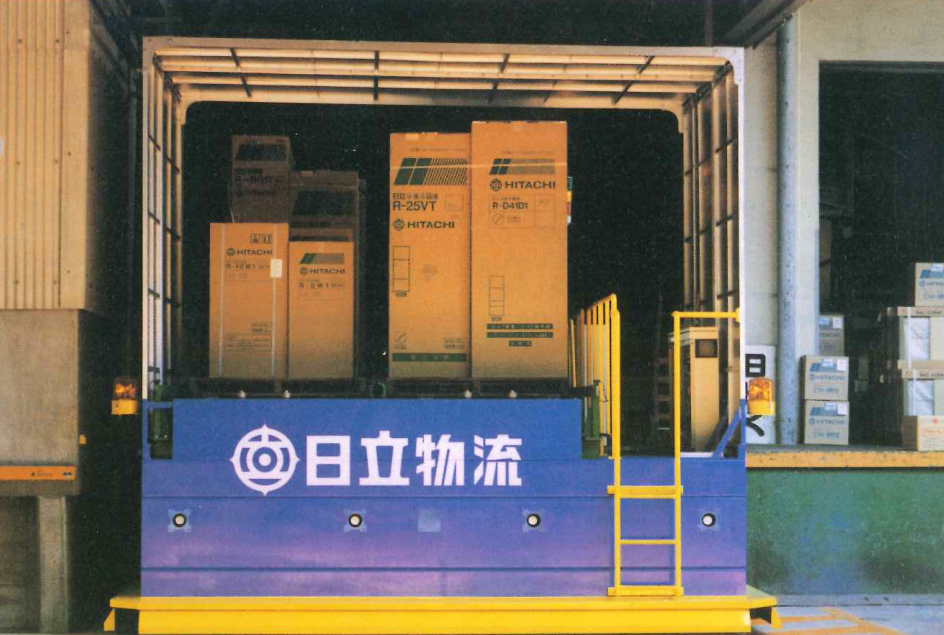
ポイント 一目にも鮮やかな日立ブルー
- 荷を一度に4パレット移動。
- 無人で自動運転が可能。
- 安全性を考慮して、入出荷ステーションからAGVS本体への移載はスイッチにて作業者が行なう。
- フォークリフト上でのスイッチ操作が可能。
- KONGO独自の技術によるオリジナルレールを使用し、安全性と耐久性を確保。
- 通常は無人・自動稼働だが、有人操作も可能。
- バンパー、センサー、パトライト、信号機等安全対策に万全を期している。
- 全天候対応型。
所感
ユーザー側で、コンセプトが初期からはっきりと決定されており、プロジェクトチームによる詳細な企画書・イメージが、メーカーである金剛(株)に正確に伝えられるという体制が整っていたことが、今回の物件で最も評価できる点です。
また、日頃から代理店の方々や関連企業の方々との密接なコミュニケーションをとっていたことも、大切な点だと思われます。お互いの信頼関係が、万が一のアクシデント発生時の、素早く親身な対応の根本になります。特に代理店である(株)正興商会殿の担当の方は、午前1時に現場に入ることさえあったということで、大変なご尽力をいただき、今回の成功の大きな原動力となりました。
物流システムに限らず、新しいシステムを導入する際に最も注意すべきことは、どのような効果を求め、そのための最善の策は何かを探りだすことです。 ややもすると、ハイテクの恩恵を目一杯に受けたい欲求に駆られ、あの機能もこの機能もと欲張ってしまうことがあります。 しかし、反対に目的を絞り込み、複雑すぎる流れは作らないことが成功を導くことになるのではないでしょうか。
(1991年8月10日刊行)